bottom pasted 3 layer cement paper bag production line - ZT1080/HD600/130
Material: Paper | Paper Type: Kraft Paper | Industrial Use: Cement | Feature: Moisture Proof |
Surface Handling: Flexo Printing | Sealing & Handle: 3 type Bottom valve | Custom Order: Accept | Place of Origin: Shandong China (Mainland) |
Brand Name: HILK | Model Number: ZT1080/HD600/130 | Power: 240KW | Air Pressure: 1.2MPA |
Color: As per customer choice |
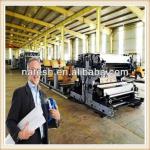
bottom pasted 3 layer cement paper bag production line
HILKhi-speed automatic bag bottom pasting machine group is based on German technology, and we fully reform the design of the equipment with most up to date international 3 dimension design software (pro/ENGINEER), and the design of the automatic production line is in accordance with the national design criteria of the People’s Republic of China. All machine parts, standardized parts and gear wheels are in metric system, 100% made in China. The main parts of the machine group are withdrawing for maintenance and calibration purpose.
A:Electric system design criteria of the bag bottom pasting machine set
The design of the electricalsystem of the machine group is in accordance with theinternational designthe whole machine group adopted variable frequency speed control.Paste-automation package units at the end of the production line in hi-tech automation,ZT1080 mainly by the type of machine and tube-type paste HD600/130 the end of two parts.Using light, machines, electricity,gas integrationsetA total of 20 multi-channelprocess,Photoelectric PLC automatic control systemprocedures completed.
B1: Cylinderformingprocessflow chart
Mill roll stand,- Automatic print unit - Automatic paper web guide - Automatic paper unwind, - Auxiliary web draw system - ,Perforation - Cross stepgluing - ,Longitude seam gluing - Tube forming - Main drive andseparation.
B2: Bottom formingprocessflow chart
High speed feeder - Perforation of the whole set - Main sack delivery - Opening the sacks,Sealing strip - Auto gluing - Sackforming - Turnining of sack bottomcutting - Packinganddelivering - Platform for storing.
C:Features of our full-automatic paper bag production line:
Flat & glued bottom with filling valve;
Different types for cement, chemicals, foods, tea, etc.
4-color automatic printing
2~4 paper layers, with one extra PE/PP film available
35~50 million bags/year
Servo system control or PLC control available, integrated with Photoelectric
Pneumatic control system, Siemens electrical system
D1:ZT1080-Technical details of Tube forming machine
Tube Length | 620-1000* mm |
Tube Width | 340-550* mm |
Paper Reel Width (Mm) | 1120 max |
Paper Reel Diameter (Mm) | 1300 max |
Compressed Air Consumption (0.8-1.0 Mpa.) | 0.7 min. (cbm/min.) |
Output (pcs/min.) | 130 min. Max. |
Equipped Power | 17.76 Kw |
Dimension (L×W×H) | 32 × 2.8 × 2.5 M |
Weight | 23.6 Mt |
Plies of Paper | 4 plies of paper +1 ply of plastic membrane |
D2.HD600/130Technicaldetailsfor Bottomer
Bag Length | 420-750* mm |
Bag Width | 380-550* mm |
Bag Bottom Width | 90-130 mm |
Bag Bottom Center Distance | 300-650 mm |
Valve Patch Cutting Length | 125-240 mm |
Valve Patch Cutting Width | 120-250 mm |
Diameter of Valve Patch Roll (Mm) | 1300 max. |
Valve Types | 3 types: |
*Half Valve | |
*Completed Valve | |
*Extruded Valve | |
Vacuum (-80 Kpa) | 260 cbm/h |
Compressed Air Consumption (0.8-1.0 Mpa) | 1.6 min. (cbm/h) |
Output (Pcs/min.) | 120 min. Max |
Equipped Power | 21.1 Kw |
Dimension (L×W×H) | 22.2 × 2.8 × 1.9 M |
Weight | 22.7 Mt |
Packaging Detail:Sea worthy plywood box suitable for multiple handling |
Delivery Detail:30days |