TL1030-Cylinder aluminum lipstick case - TL1030
Material: Aluminum,Aluminum Custom lipstick case | Usage: Cosmetics | Cosmetic Type: Lipstick | Surface Handling: Screen Printing |
Place of Origin: Jiangsu China (Mainland) | Brand Name: Custom lipstick tube packaging design | Model Number: TL1030 | Name: Custom lipstick case |
Shape: Cylinder custom lipstick case |
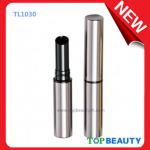
Cylinder aluminum custom lipstick case
Aluminum anodizing metal shinny surface,
50/50 for the base and cap.
Product Specifications
Product Description | Cylinder aluminum custom lipstick case |
Category | Custom lipstick tube packaging design |
Sub-Category | Custom lipstick tube packaging design |
Item Number | TL1030 |
Decoration | Silk Screen, Spray Coating, Anodizing |
Shape | Cylinder Round |
Material | Aluminum for cap and base |
Volume | Standard cup size |
Dimension | D14.16mm*H93.4mm |
Manufacturing Process | Anodizing aluminum and injection for the mechanism |
Packaging information | Carton box with layer |
MOQ | 10,000 pcs |
FOBPort | Shanghai |
Our Facilities
Injection molding
Our comprehensive range of injection molding machines gives us the flexibility to fulfil the diverse scope of our customers’ requirements. Processes we carry out include: conventional injection molding, over-molding and insert molding and clean room molding.
We select and source high-quality materials from proven suppliers, and have experience in processing most thermoplastics on the market.
Our machines
We have 30 injection molding machines, ranging in size from 100 to 400 tonnes, providing us with the flexibility we need to meet our customers’ individual requirements. Our engineering team provides the expertise and capability needed to maintain the machines on a day-to-day basis, using a TPM programme to maximise machine utilisation and reliability.
Assembly
Our clean room assembly areas are designed and laid out to provide the best possible material flow and are set up for standardised operations. We use IE to analysis to set standard times and monitor output, enabling us to deliver consistently high-quality plastic injection moulded assemblies for all applications.
Tooling workshop
Our in-house tooling workshop is equipped with the latest technology, and is staffed by experienced mould toolmakers who work closely alongside our design team. Our tooling manufacturing capabilities extend from soft prototype tools through simple single impression P20 steel tools, to fully hardened steel multi-cavity full hot runner tools. The tooling workshop also fabricates prototype and development mould tools and jigs, fixtures and gauges for production.
...
Packaging Detail:Carton box with layer lipstick case |
Delivery Detail:40 days after get the confirmation of PO |